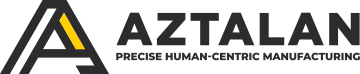
New Equipment Highlights Commitment to Better Service Our Customers Part of our commitment to continual improvement is to make investments in machines that will allow us to better service our cust ...
Read MoreOften welding comes to mind when you think about joining metal components. However, two other methods are often preferred in certain circumstances: soldering and brazing. Instances where these methods ...
Read MoreWhy Being An Employee-Owned Company Matters To Our Customers Aztalan is a 100% employee-owned company. This means that our employees obtain ownership of the company through a privately held Employee S ...
Read MoreThe pandemic and resulting supply chain constraints set in motion a 5-year strategic plan for GE Healthcare to change the relationships they have with their suppliers. At the foundation of the change ...
Read MoreAn Overview of Soldering Services Precision soldering services are used to join two or more pieces of metal together in various standard and complex applications. The most common ways to join metals ...
Read MoreCNC Milling and Turning: Which is Best for Your Machined Parts? Since the rise of computers, CNC machining has steadily replaced manual milling, resulting in higher quality parts with tighter toleranc ...
Read MoreSome manufacturing customers will outsource their machined components to a machine shop and then have their own engineers clean and put together subassemblies. However, it is much more efficient to ha ...
Read MoreBringing any product to market rarely is without challenges. Engineers of products or components that are CNC machined must take extra care to design products correctly. CNC is a subtractive process; ...
Read MoreFrom simple prototypes to complex technical and medical components, CNC machining is a favored production method for a variety of projects due to its versatility, premium quality, and design capabili ...
Read MoreThe use of industrial robots has seen a boom in recent years and is expected to continue to grow. They have become an integral part of many manufacturing processes, whether used alongside humans to p ...
Read MoreWhat is Automotive Machining? The modern automotive industry was born of innovation and automation. In 1913, Henry Ford revolutionized the industry with the use of an assembly line in automobile prod ...
Read MoreExpert machinists have the capabilities and skills to transform your chosen CNC materials into a machined part precisely machined to meet your unique requirements. CNC machining is swift and accurate ...
Read MoreCNC machining is a vital manufacturing process contributing to major innovations in the aerospace industry. From aircraft parts and prototypes that empower modern turbines to complex spacecraft compo ...
Read MoreOne of the valuable aspects of the services provided at Aztalan Engineering, Inc. is our commitment to precision and accuracy with every part and component we manufacture. While some companies offer p ...
Read MoreIn many different industries from parts and components for firearms to robotics and medical devices, precision is critical. Not only is precision important for the functioning of the device or system, ...
Read MoreRecently Aztalan Engineering was able to adopt a local family through Christmas Neighbors with money raised from Penny Wars during our October ESOP Month. We’re thankful to have the ability to support ...
Read MoreIn order to be competitive in today’s world, an original equipment manufacturer or OEM must utilize advanced technology. One such technology is CNC prototyping. With it, a company that needs thousands ...
Read MoreHaving an idea for a new medical device that can treat a condition, restore mobility, help to alleviate pain or discomfort or to give someone a chance to get back to a healthy life is an amazing oppor ...
Read MoreAt Aztalan Engineering, we offer a variety of precision-machining services including CNC turning services. Before choosing what type of services your company is looking for, it may be of some help to ...
Read MoreMedical device prototyping is a process that is crucial to medical device development and helps to ensure quality and proper function of a design before the device is used in its final application. At ...
Read MoreBefore WWII, making metal parts was labor-intensive and inexact. After, John T. Parson developed the idea of numerical control (NC) machines, which used punched tape to store data that tape readers wo ...
Read MoreUltrasonic Cleaning: When Need Gentle, Effective, and Deep Cleaning Ultrasonic cleaning is often used in metal manufacturing to clean parts before another process, such as coating or painting. It can ...
Read MoreCNC Swiss turning or swiss machining is a high-precision method to cut tight-tolerance, small, intricate parts using a CNC Swiss-designed lathe. Short History of Swiss Machining Swiss machining has an ...
Read MoreNew CNC Swiss Machine Increases Capacity – Supports Faster Lead Times And Competitive Pricing Aztalan is excited to announce the addition of a DMG Mori Sprint 20|8 automatic turning machine to our a ...
Read MoreThe Full Guide to Machine Shop Quality Control When it comes to CNC machined components, precision is essential to your application. Working with a partner that you know can make the parts you need p ...
Read MoreHow Mechanical Engineering Consultancy Services Can Help Your Design Team Mechanical engineering consultancy services can help you tackle challenges from design to production. While we do not design ...
Read MorePlastics have become an indispensable material for manufacturing countless products, from cheap toys to highly engineered spacecraft components. The variety of plastics available makes them suitable ...
Read MoreUltrasonic cleaning is an essential part of Aztalan’s precise, full-service CNC parts and equipment manufacturing and assembly services, as it allows us to deliver finished metal products cleaned to ...
Read MoreCNC material selection is an integral part of the project planning process. The material chosen will affect the final component’s price, longevity, and suitability for your application. Deciding whic ...
Read MoreThe Aerospace Sector Takes Off Again The COVID-19 pandemic wreaked havoc on the aerospace industry, particularly on commercial airlines. The pandemic grounded two-thirds of the world’s passenger jet ...
Read MoreCombining the power of technology with precision machinery, CNC machines are capable of producing a variety of precision metal parts across industries. Following computer instructions instead of manu ...
Read MoreThe Importance of Choosing a Reliable Machined Parts Manufacturer CNC machining is a staple of modern American manufacturing due to its extreme accuracy, automation, and cost-effectiveness. If your bu ...
Read MoreSwiss Turning is the Key to Tight Tolerances Swiss turning is a specialized process wherein manufacturers make small, high-precision and tight tolerance parts for various industries. These industries ...
Read MoreCNC machining requires accuracy and precision. Accuracy refers to the closeness of a measured value to an actual value. For example, an accurate machine programmed to remove 0.1 in of material will r ...
Read MoreThe oil and gas industry uses specialized equipment fluid handling systems to deliver natural resources to market. They are often stored and moved under extreme pressure and temperatures during extrac ...
Read More